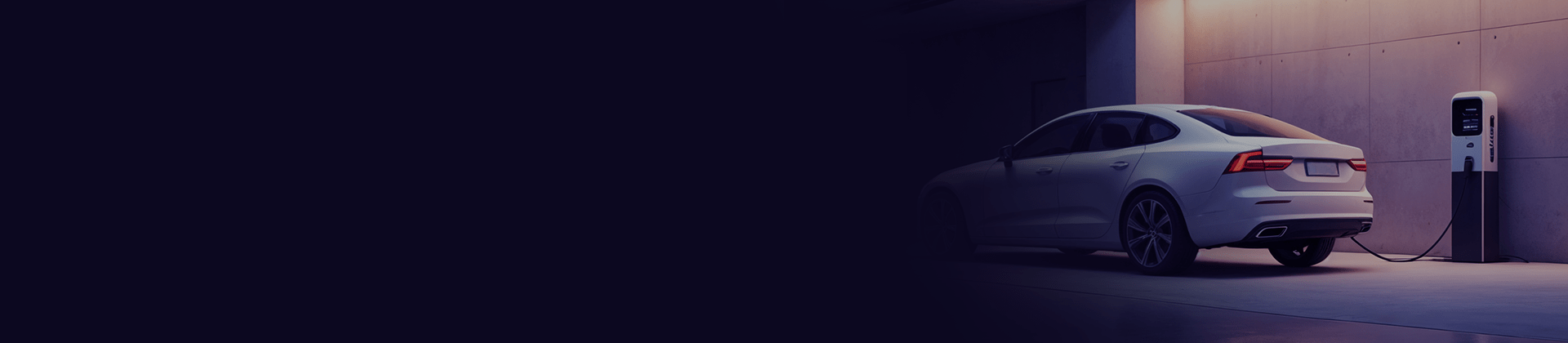
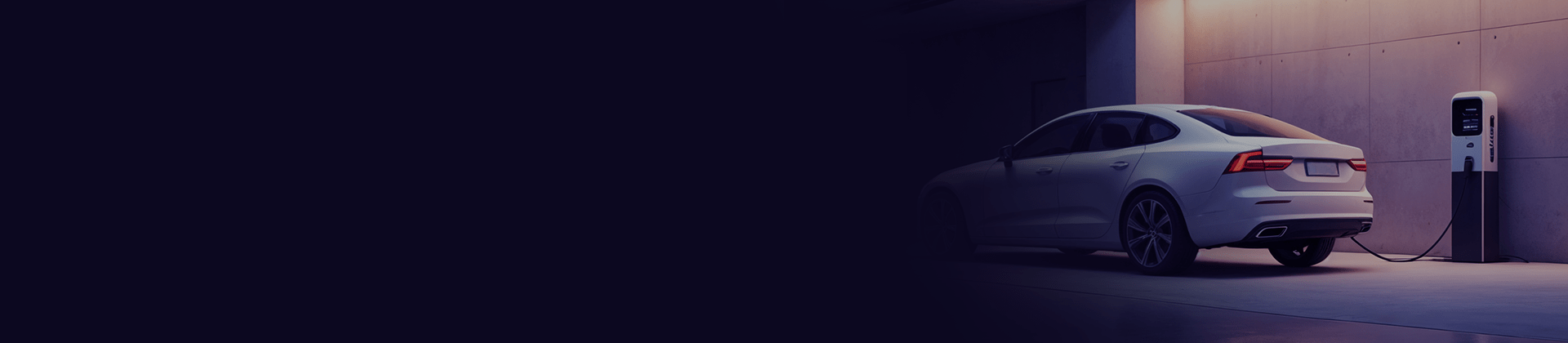
a1qa quickly selected experienced QA engineers who strengthened the expertise of our internal QA team, analyzed the existing QA processes, unified and customized them to achieve better work results.
a1qa’s responsible attitude to our needs, strong technical skills, and well-established communication allowed us to promptly address emerging QA issues and attain the desired business outcomes.
Head of QA at Business Systems Department
Committed to transforming sustainable transport, the client uses proprietary hardware, software, and lightweight composites to design and build affordable, customizable electric vans, buses, and cars that advance the global shift to zero emissions.
As business was scaling rapidly, the client’s core concern was seeking proficient QA specialists with sufficient technology and domain knowledge to close required expertise gaps. Faced with tight deadlines, the company could not afford a lengthy search to hire the ten‑plus specialists it required.
Therefore, the client turned to a1qa to ensure impeccable operation of car systems, a CRM, ERP, and web and mobile B2B applications, such as a bus park management platform, customer care portal, screen content management platform for public transport, app for drivers with gamification elements amongst others.
By the time a1qa joined, the client’s in‑house team was already testing software across three core streams: Technology (car systems), Business Systems (CRM, ERP, and other internal products), and Digital (customer‑facing web and mobile apps).
After quickly diving into the project context and gaining a clear understanding of the client’s domain, needs, and concerns, a1qa staffed the team rapidly and with a high success rate of candidates passing rigorous technical interviews.
a1qa’s flexibility in delivery models played an important role in adapting to the project’s complexity. In some areas, the company operated in a team augmentation model, seamlessly integrating with the client’s existing workflows. In others, a1qa provided a fully managed team, taking ownership of quality control processes and delivery milestones.
Therefore, a1qa smoothly integrated into mixture of Scrum and Kanban processes. Responsibilities ranged from functional testing to supporting QA automation, always aligned with the evolving needs of different directions on the project.
This was the most difficult subproject, where full-stack QA engineers were directly immersed in the intricate and demanding task of car systems testing, navigating the profound complexity inherent in modern vehicle architecture. Experts ensured their failsafe operation through integration testing and test automation.
During the integration testing phase, a1qa’s engineers focused on verifying the functionality and reliability of a complex automotive communication platform — a central hub designed to coordinate various vehicle subsystems such as lighting, start-stop systems, and rain sensors.
Their work involved validating how the communication module processed and transmitted output signals to connected components, ensuring seamless integration and responsiveness. By crafting detailed test scenarios that mirrored real-world automotive conditions, they employed both physical modules and emulated environments to rigorously assess system behavior.
This approach enabled comprehensive testing of both individual components and their interactions within the integrated platform, ensuring robustness, accuracy, and readiness for real-world deployment.
As part of the integration testing effort, QA engineers developed a robust suite of automated tests in Python to validate the behavior of the software. Automated scripts were executed on dedicated test stands, enabling efficient and repeatable verification of how it processed and relayed signals across integrated subsystems. Test automation significantly accelerated the testing process while maintaining high accuracy and coverage.
In addition to providing deep QA expertise, a1qa created a bespoke training program to prepare candidates for testing complex automotive systems. Engineers had to prove proficiency in Python, Linux, physics, web services, and test design before joining the project.
To make sure CRM, ERP, and some other internal portals were running like clockwork, a1qa ran functional, performance testing, and test automation.
The QA team joined test plans and test documentation creation, establishing clear guidelines for the entire testing effort. They then focused on new feature testing, rigorously evaluating newly implemented functionalities to confirm their adherence to specifications. Throughout QA cycles, they diligently managed test data to simulate real-world scenarios and performed defect validation and logging whenever issues arose. Finally, they conducted detailed logs analysis to pinpoint root causes and ensure overall stability.
To prevent slowdowns that could negatively impact sales cycles, customer support efficiency, and overall business productivity, a1qa proceeded with performance testing. Engineers developed detailed test plans, outlining the scope and strategy for evaluating key performance metrics, such as response times for lead creation, data retrieval, and report creation. A significant part of their efforts involved extensive load testing, which rigorously pushed the software to its limits to uncover any performance limitations when handling a large volume of concurrent users or complex queries.
To achieve efficient, high-quality releases and accelerate QA cycles, a1qa spearheaded test automation efforts. This involved creating extensive automated test scripts, from unit test cases validating individual components to broader end-to-end scenarios. Specialist closely collaborated with development and DevOps teams, ensuring test automation was fully woven into the continuous integration and deployment pipelines.
In this stream, the team performed manual and automated testing of web and mobile solutions that streamline key business operations, from omnichannel customer support to fleet logistics and management.
Responsibilities of QA engineers encompassed end-to-end validation of user scenarios and meticulous test management to coordinate testing efforts across platforms. By aligning test coverage with real-world use cases and business goals, they ensured that each application delivered a seamless and consistent user experience. This work bridged the technical and customer-facing layers of the system, contributing to the overall stability, usability, and readiness of the integrated digital ecosystem.
To ensure fast validation of functional scenarios, support continuous delivery, and improve overall software stability within the integrated automotive ecosystem, engineers developed and maintained automated test suites. This helped accelerate delivery speed, reduce manual effort, and minimize regression risks.